First 3D-Printed Headdress Prop Debuted in the Hit Drama "Joy of Life 2" -- Designed by a Milab PhD student
- 海鹏 米
- May 22, 2024
- 5 min read
(Interviewee: Yao Zhihao; Interviewer: Li Xueqing)
In the recent hit television drama "Joy of Life 2", fans will witness the grand wedding scene between Fan Xian and Lin Wan'er. Lin Wan'er's wedding headdress, distinct from traditional styles, boasts a transparent material and is purportedly the first-ever headpiece prop in Chinese television history entirely designed through digital modeling and 3D printing.
Milab's Ph.D. candidate, Yao Zhihao, serves as the digital designer behind this headdress. As the drama premieres, we had the opportunity to interview Yao Zhihao to delve into the behind-the-scenes story of this design.
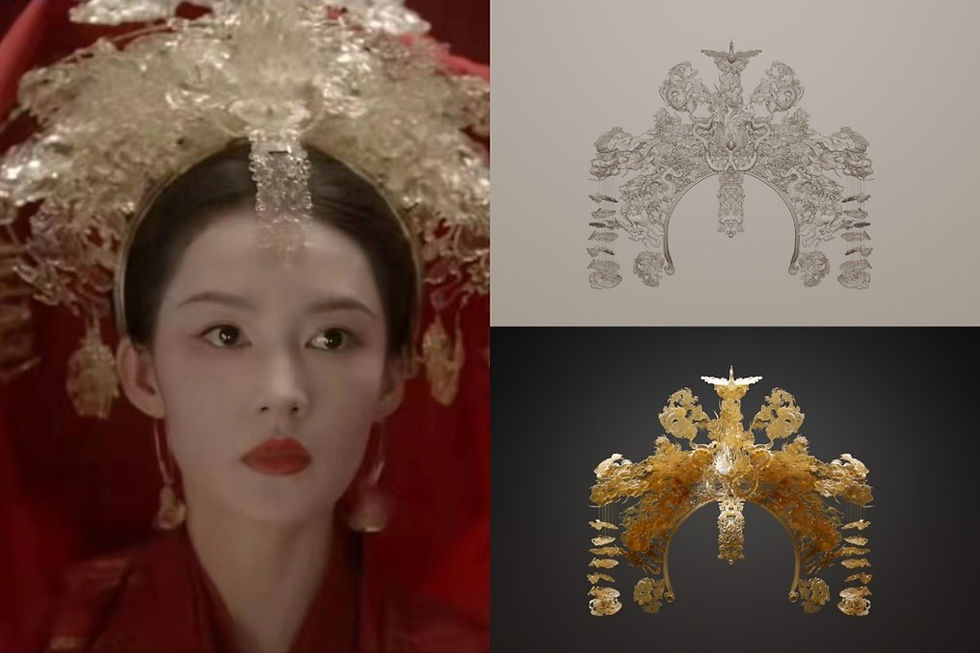
Q1. What was the initial impetus for your involvement in this project?
The impetus originated from the collaboration between the production team of "Joy of Life" and Professor Bi Ran from the Beijing Film Academy, who engaged in discussions with me regarding the production of relevant props for the series. Professor Bi Ran, also an alumna of the Department of Textile and Fashion Design at Tsinghua University's Academy of Arts & Design, had previously collaborated with our laboratory on projects such as the MOJA robot. Thus, we embarked on the design of the headdress for "Joy of Life" in a collaborative capacity. Initially, Professor Bi Ran primarily facilitated conceptual design and liaison, while I focused on modeling and the practical implementation of 3D printing.
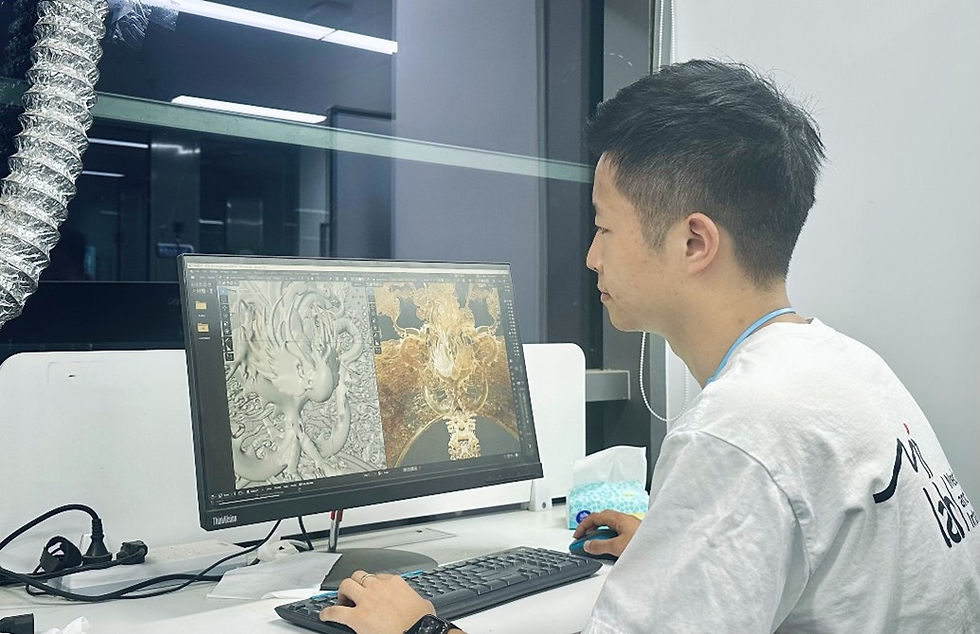
Q2. Why did you consider using 3D printing and a semi-transparent texture in designing the headdress, and how did you take into account the characteristics of Lin Wan'er's grand wedding and the background of the storyline?
We were tasked with designing a headdress for actress Li Qin's portrayal of Lin Wan'er in the grand wedding scene. Recognizing "Joy of Life" as a period drama with elements of time travel, the director expressed a desire for the incorporation of modern elements rather than strictly adhering to traditional hairpins. Given our limited production timeline of three days, we ultimately opted for 3D printing as the preferred method.
Firstly, the choice of a fully transparent design stemmed from prior experimentation with transparent materials in 3D printing. In the realm of 3D printing, semi-transparent or fully transparent materials are relatively less common compared to more conventional 3D printing materials. Through previous trials, we discovered that the combination of traditional hair ornaments with transparent 3D printing techniques yielded remarkable results in crafting headwear. Hence, we decided to continue this design approach for Lin Wan'er's wedding headdress, portrayed by Li Qin.
Secondly, the director sought the integration of modern elements into the hair accessory design. In ancient times, transparent materials were considered luxurious and rare, thus semi-transparent materials better aligned with the setting of "Joy of Life."
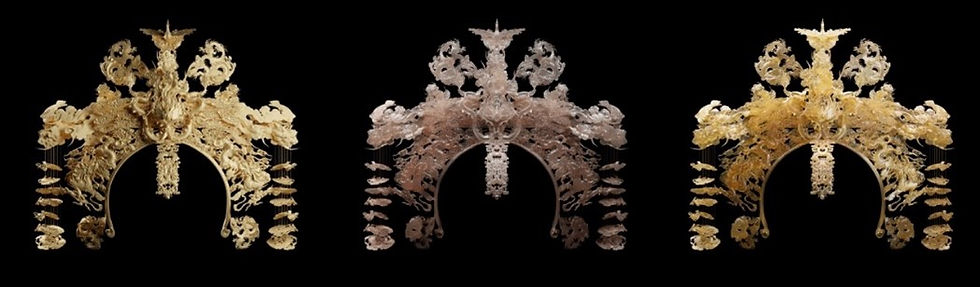
Q3. What challenges did you encounter during the headdress design process?
The primary challenge revolved around time constraints. With only three days allotted for the project, including the time required for model printing and transportation, we were left with a mere day for the design phase. To expedite the process, we utilized AI assistance for rapid conceptualization in the initial stages of design. Integrating various traditional Chinese elements such as dragon motifs, cloud patterns, and floral and bird patterns, we sought to enrich the aesthetic of the headdress.
An anecdote emerged during production: initially unaware of actress Li Qin's head circumference, crucial for the structure of the headdress resembling a headband, Professor Bi Ran volunteered to serve as Li Qin's head model. We scanned Professor Bi Ran's head data to aid in modeling, later adjusting and modifying it upon obtaining Li Qin's head circumference. This posed a significant challenge, as time constraints allowed for only one opportunity to finalize the design; once printed, adjustments to the headdress's dimensions were no longer feasible.
Despite the visually intricate and voluminous nature of the headdress, its weight remained relatively light due to the use of transparent resin as the printing material, highlighting one of the advantages of 3D printing.


Q4. I heard that this headdress might be the first in the domestic film and television industry to be entirely digitally modeled, 3D printed, AI-assisted, and feature a fully transparent texture. What impact do you think such a design might have on props in Chinese television dramas?
In the field of film and television prop production, 3D printing is increasingly prevalent, showcasing a trend of continual advancement. Several key aspects characterize the production process of this headdress: firstly, it incorporates intricate Chinese elements; secondly, its design process involves AI assistance, culminating in 3D printing through photopolymerization. The precision and complexity of the final product are notably high. This manufacturing process not only utilizes semi-transparent or fully transparent materials but also supports various spray coatings and modifications, offering a high degree of freedom. Overall, this constitutes a rapid manufacturing method.
In traditional production processes, crafting complex hair accessories within 1 to 3 days is challenging. Compared to traditional techniques, this method presents a new approach to prop production in the film and television industry.
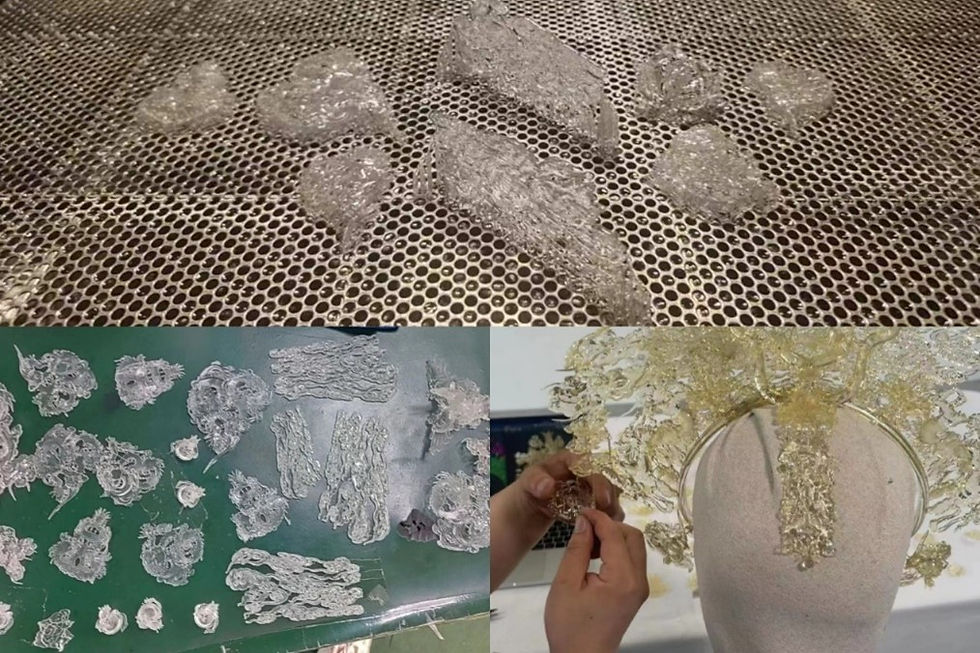
Q5. Could you share some interesting experiences from behind-the-scenes production?
One particularly memorable experience was the collaborative relay. Our greatest challenge was time constraint, as previously mentioned; factoring in printing and transportation time, we had only one day for design. On the eve of the design day, Professor Bi Ran and I discussed our roles in advance. She organized the design requirements and prepared numerous AI-assisted conceptual drawings, while I prioritized rest to prepare for the intensive modeling task the following day. Throughout the design process, our plans underwent continuous revision, iteration, and modification, rendering it a non-linear endeavor. AI provided numerous reference images to aid our design process.
Another intriguing aspect was our reliance on AI-generated concept drawings for modeling. However, the structural complexity of AI's drawings made them subject to constant scrutiny and refinement in real-time. Professor Bi Ran and I engaged in iterative modifications almost instantly after discussions, creating a sense of intellectual collision and serendipity.
Q6. If the headdress you designed could become a fashion item or a specific craft in reality, would you like to try designing other types of props?
That's an excellent question. In fact, I experimented with a series of jewelry pieces afterward, primarily for my girlfriend to try on. It was my first foray into the realms of jewelry and props, and in the process, I discovered some new perspectives.
Traditional jewelry making typically relies on artisans assembling existing materials by hand, a time-consuming process that often struggles to produce novel designs, with remolding posing significant challenges. However, these hair accessories, crafted through a combination of 3D printing and AI assistance, were actually designed by my girlfriend, who comes from an engineering background. The results were stunning (verified by the interviewer). The semi-transparent material naturally exudes a sense of sophistication. These accessories, blending ancient design paradigms and elements with contemporary craftsmanship, truly captivated me. Furthermore, the inclusion of AI in the design process makes it engaging for a broader audience. I intend to continue exploring and experimenting in this field.
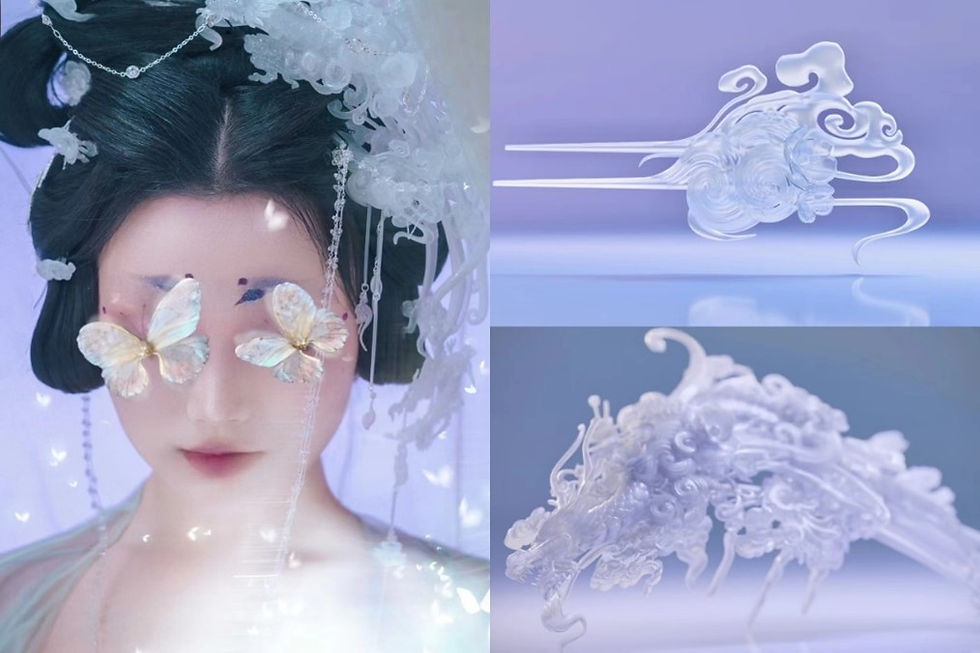
Conclusion: Yao Zhihao shared the design process of the crucial props in "Joy of Life 2", particularly highlighting the impressive utilization of AI assistance, fully digital modeling, and photopolymerization printing within an extremely short timeframe. His insights serve as inspiration for our fellow students engaging in design work.
Authored by: Li Xueqing
Image provided by: Yao Zhihao
Comments